LIFTING OPERATION STANDARDS & COMPLIANCE
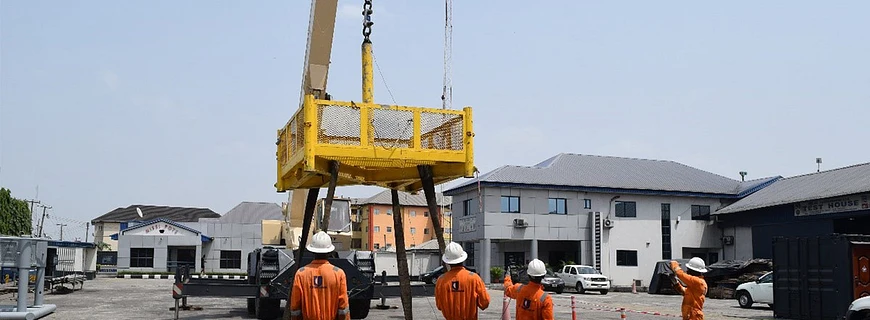
Lifting Operation Standards – Formally-established Requirements
Lifting operations do have the potential to cause incidents, from uncontrolled movement of loads and dropped objects impacting people, assets, and the environment in proximity of the operation. The management of lifting operations through formally established requirements – operational standards, ensures that risks of lifting incidents are reduced and/or eliminated. The standards that covers lifting operations are influenced by primary legislation – Acts, Regulations and Directives, depending on the location the lifting equipment is manufactured and used or where the lifting operation is taking place.
Acts
Set and passed by Parliament as law, it contains legal policies that can only be amended by another Act of Parliament.
- Health and Safety at Work Act 1974 – Employers have a duty to ensure, so far as is reasonably practicable, the health, safety, and welfare at work of all their employees.
Regulations
Referred to as ‘secondary legislation’ and contains guidelines that controls how provisions of the Act are applied.
- Lifting Operations and Lifting Equipment Regulations 1998 (LOLER) – Regulations covers lifting equipment and lifting operations and places duties on people and companies who own, operate, or have control over lifting equipment.
- Provision and Use of Work Equipment Regulation 1998 (PUWER)– Regulations places responsibilities on people and companies who own, operate, or have control over work equipment.
In addition to complying with LOLER, companies who own, operate, or have control over lifting equipment should also comply with all the relevant aspects of PUWER and any other applicable health and safety law.
Directives:
Represents a form of legislation that is ‘directed’ at the Member States and sets out policies which needs to be met.
- The Machinery Directive 2006/42/EC– Sets out the essential safety requirements relating to the design and construction of machines placed on the market of Member States.
Lifting Policy
Lifting Policy is a high-level statement of management objective that contains the ‘what to do’ information required to produce and ensure safe lifting operations. It represents a statement of expectation that is enforced by standards and implemented by procedures.
Compliance is a non-negotiable element and means conforming to a policy, standard or procedure.
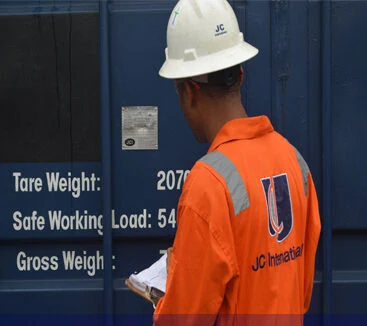
LOLER – How to be Complaint with Lifting Regulations
The lifting operation shall detail a scheme of compliance with the Lifting Operations and Lifting Equipment Regulations 1998.
The LOLER regulations require that all lifting operations involving lifting equipment must be
- Properly planned by a Competent Person
- Appropriately supervised
- Carried out in a safe manner.
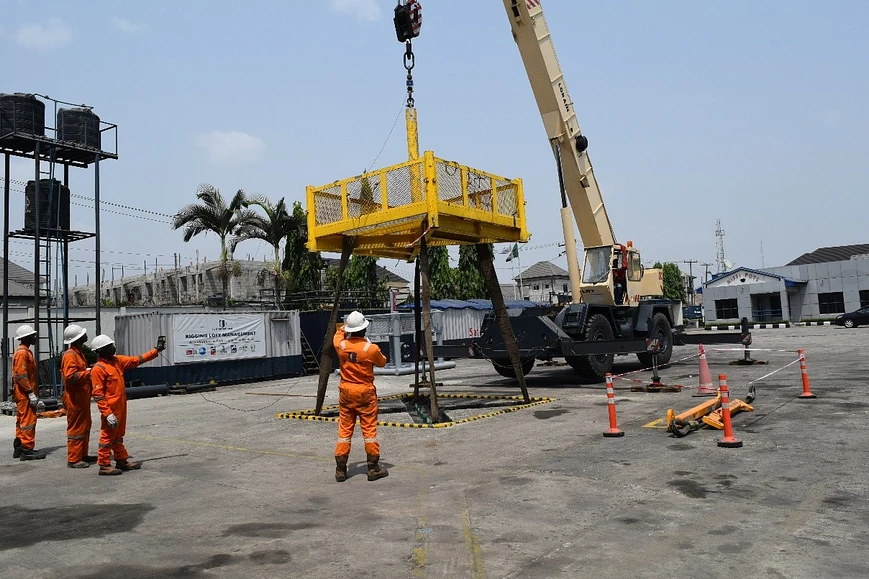
It also requires that all equipment used for lifting is
- Designed, manufactured, and certified fit for purpose
- Appropriate for the task
- Suitably marked with suitable maintenance recorded and defects reported.
Where lifting operations involving lifting equipment is undertaken you must:
- Plan them properly
- Utilising people who are deemed to be competent
- Supervise them appropriately
- Ensure that they are carried out in a safe manner
LOLER – What Lifting Equipment is covered?
The LOLER regulations applies to work any equipment only. The following criteria applies also:
- Lifting equipment used to lift and lower a load
- Equipment that attaches a load to a lifting equipment
- Equipment that supports, fix or anchor equipment used to lift or lower a load
However, some work equipment may not be subject to LOLER’s specific provisions. However, when used at work, the provisions of PUWER still apply to all equipment (including selection, inspection, maintenance, and training).
Standards:
- Standards are formally established requirements regarding processes, actions, and configurations.
- Standards are finite, quantifiable requirements that satisfy desired conditions to be met.
- Exceptions are always to Standards and never to Policies. If a standard cannot be met, it is generally necessary to implement a compensating control to mitigate the risk associated with that deficiency.
Standards or sometimes referred to as Codes of Practice, are used to establish the technical detail for the safe use and operation of the lifting equipment in the form of guidance and recommendations. British Standards produced by the British Standards Institute (BSI) group, issues technical specifications that promotes safe use of lifting equipment and ensures compliance with LOLER and PUWER. The main ones are listed below Table 1.

Lifting Standards:
Reference
Standards
BS 7121 -2 -7
Code of practice for the safe use of cranes – Inspection, maintenance, and thorough examination – Overhead travelling cranes, including portal and semi-portal cranes, hoists, and their supporting structures
BS EN 13411 – 1
Terminations for steel wire ropes. Safety. Thimbles for steel wire rope slings.
BS ISO 4309
Cranes. Wire ropes. Care and maintenance, inspection, and discard
BS EN 14502-1
Cranes. Equipment for the lifting of persons. Suspended baskets
BS EN 13414
Steel wire rope slings. Safety. Slings for general lifting service
BS EN 13889
Forged steel shackles for general lifting purposes. Dee shackles and bow shackles.
BS EN 14502
Cranes. Equipment for the lifting of persons.
BS EN 1492-1
Textile slings. Safety. Flat woven webbing slings, made of man-made fibres, for general purpose use.
BS EN 12079-1
Offshore containers and associated lifting sets. Offshore containers. Design, manufacture and marking
BS EN ISO 10855-1
Offshore containers and associated lifting sets. Design, manufacture and marking of offshore containers
Table 1 Lifting Standards
Compliance
As explained, lifting standard, guidelines and procedures are written to comply with legislations, regulations, and directives. Companies who own, operate, or have control over work equipment must prove they comply regulations by demonstrating they have a robust safety management system that contains accepted codes of practice, guidelines, and procedures.
Still not sure how to demonstrate compliance?
The Answer:
Due to the overwhelming challenges of identifying, interpreting, and implementing latest standards and regulations, it is extremely vital that attention is giving to the selection of a reputable service provider with the qualification, breadth of experience and track record.
At JC International, we recognize these challenges and we are happy to offer our expertise in helping you establish a strategy to ensure you comply with standards and regulations. LOLER audits are performed by experienced and qualified Competent Persons with sufficient skill and knowledge in the relevant codes, standards, and regulations.
Our focus is to provide a world-class service to ensure that our clients as duty holders, can use their lifting equipment and perform lifting operations safely whilst also demonstrating compliance with national and international regulations.
Leave a Reply