LIFTING OPERATION PROCEDURE
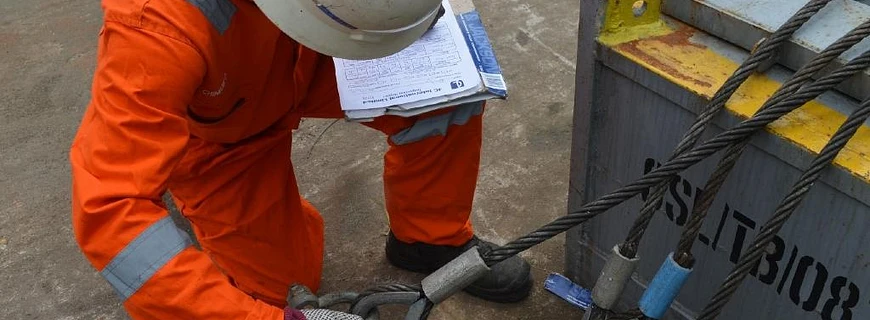
Lifting Operation Procedure Guide to Effective Implementation
In previous blogs, we discussed the origin of Lifting Procedures from a hierarchy containing Acts, Regulations, Standards and Policies. Lifting Policy is a high-level statement of management objective that contains the ‘what to do’ information required to produce and ensure safe lifting operations. It represents a statement of expectation that is enforced by standards, rules and references and divided into people, plant, and processes.
In this blog, 5 key guides that will enable effective implementation of Lifting Operation Procedure for a company that conducts lifting operational activities will be discussed.
Lifting Procedures describes the ‘how to’ information and contains templates that are required to produce and ensure safe lifting operations. The document enables the implementation of the Policy and represents a statement of expectation. It is also divided into people, plant, processes, forms, and performance requirements.
Incidents and accidents continue to occur during Lifting Operations i.e. uncontrolled loads and dropped objects, resulting in serious injuries and sometimes fatalities. Having a robust Lifting Operation Procedure ensures that these operations are carried out in a safe manner, carefully planned and undertaken by competent people. An effective Lifting Operations Procedure should define the responsibilities, training, competencies, and assessment of those involved in lifting operations. It should also set out a structured approach aimed at ensuring that such operations are adequately risk assessed and systematically planned. Key guides below.

1. Structure
As discussed above, it is important for the procedure to be structured essentially to address 5 key categories namely:
- People – everyone involved in lifting operations should have specific roles and responsibilities and must be able to demonstrate the required level of competence to undertake the assigned role.
- Plant / Location – this specifies the plant, area, or location the procedure applies to. This is important in situations where work activities are carried out by company employees and external Third-Party Contractors. There must be agreement and alignment with company lifting procedure and Contractors must demonstrate its procedure is equivalent or accept company lifting procedure as primacy.
- Process – steps, workflow, and flowchart must be rigid with various levels of responsibility and accountability for lift operation planning and approvals. This process must be repeatable, recorded, and adaptable for any type of lifting operation.
- Forms – lift plan templates, risk assessments, toolbox talks, and feedback checklists are necessary elements of the procedure.
- Lifting Equipment Requirements – shall be designed to the appropriate code, standards, and local regulation requirement. All lifting equipment must be of suitable strength and stability for the purpose to which it is to be used.
2. Ownership
Another key guide to effective implementation includes ownership of the document and its hierarchy. The production, ownership and use of the lifting procedure must be managed by the appropriate department or office of the organisation. The document must be listed and available as part of other Safety Management, Business Management and Document Management System documents the organisation holds. The criticality of the document must be specified as well as the person responsible for its implementation.
3. Control
As discussed above, it is important for the procedure to be controlled from a single source or process due to the level of criticality and importance. Any formal review, approval, distribution, and modification of the Lifting Operation Procedure must be controlled through a documented process. The process or system shall be used to receive, track, manage and store different versions of the procedure. The lifting operation procedure must include a legal disclaimer or warning regarding use and distribution of uncontrolled copies of the procedure.

4. Response to Change
Change is inevitable and necessary to meet differing circumstances, make required improvements or respond to emerging conditions. The Lifting Operation Procedure and processes contained within it may require changes due to feedback and/or lessons shared from incidents, changes in other Acts, Regulations or Policies, changes brought about by the Industry tests (referred to as ‘Industry Best Practice’) and changes within the organisation that owns the procedure. Careful consideration must be given to the environmental and safety implications that result from any change. This means the Lifting Procedure must include a process set out by the organization, to manage any changes or deviations from the requirements contained therein.
5. Periodic Review
As a controlled living document, the Lifting Operations Procedure must be subjected to a periodic review to ensure that it keeps up to date with regulations, technology, and industry best practices. The procedure should grow and adapt with the organisation and reduce the risk incidents from outdated practices. Generally, Lifting Operation Procedures should be reviewed every 1 to 3 years with most organisations relying to a 2 yearly review cycle.
The organisation (duty holder) has a responsibility to ensure that lifting operations are carried out safely. One of the ways to do this is to have a robust Lifting Operation Procedure that must cover (as a minimum) the 5 key guides discussed above. By doing this, they are ensuring compliance with the Lifting Operations and Lifting Equipment Regulations LOLER 1998, the Health and Safety at Work Act 1974 and other National and International Regulations.
At JC International, our focus is to provide a world-class service to ensure our clients as (duty holders), can demonstrate compliance with regulations and ensure their Lifting Operation Procedure is fit for purpose, standardised, meet legal requirement and consistent across all operational asset. With our comprehensive accreditation and professional memberships, we are uniquely positioned and able to tap into industry best practices and knowledge base which represents a significant foundation for procedure reviews and updates.
Leave a Reply