CASING AND TUBING INSPECTION
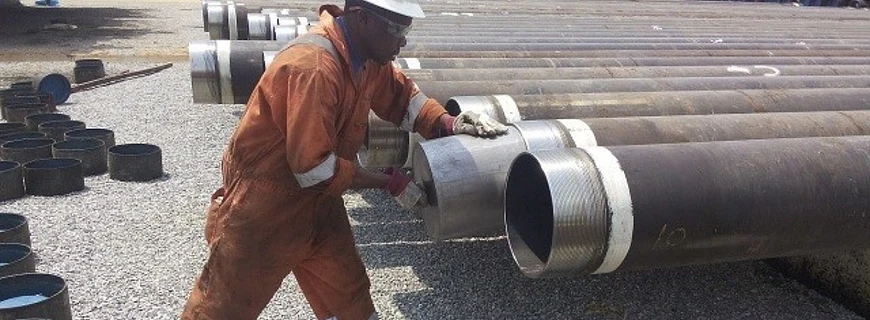
Casing and Tubing Inspection
Tubing inspection consists of electromagnetic inspection of the tube to locate internal and external pitting, cuts, and gouges that will be detrimental to the integrity of the pipe. The electromagnetic inspection utilizes the same unit that is used for the drill pipe inspection. Tube inspection just like thread inspection is used to establish the useability of threads for further use. Tubing is also used to locate any restriction that is located inside the tube which would not allow passage of tubes to be run inside the tube during production. The tubing sizes vary on certain conditions.

API RP 5A3 provides recommendations and methods for testing thread compounds that are expected to be used on threaded casing and tubing connections. The tests are used to outline the critical performance properties of the physical and chemical characteristics of thread components in laboratory conditions. API RP 5A3 specifies recommendations for new testing and inspection of oil country tabular goods (OCTG). This standard covers the technology that is used in commonly applied in field inspection.
Casing and tubing are the most important parts of a well construction. Oil wells are expected to possess strength and functional ability. Casing and tubing are essential to ensure that defects or wear do not prevent the tubing from performing below expectations. The casing is a major component of a well. It is a tabular steel product that is used to line the wellbore and prevent contamination of water sands, isolate water from producing formations, and to also control well pressures during drilling and production. The casing is important in that it provides locations for the installations of blowout preventers and production tubing.
Some factors to be considered for casing and tubing inspection
There are certain factors that need to be considered for casing and tubing inspection. They include:
Visual factors: The outside of the tubing joints must be inspected thoroughly to ensure that they are free from any mill defects such as seams, slugs, pits, cuts, and cracks. The connection should be checked for defective threads and seals.
Hydrostatic: This is a common inspection method that is used to check the tubing body and joint internally with the use of water. The test pressures are usually based on 80% of the internal yield. A more stringent test of the joint is obtained using nitrogen with a helium tracer rather than water.
Electromagnetic: To detect pits, or longitudinal defects in the pipe body, electromagnetic search coils which are known to find magnetic flux leakage are always used.
Magnetic particle: The magnetic inspection methods which comprise both dry and wet methods are used to induce a longitudinal or transverse magnetic field in the tubing and magnetic iron particles that are dusted on the tubing align at defects. This type o0f method is used to check the outside surface of upset and the end area region for the presence of any crack.
Ultrasonic: The Ultrasonic high-frequency sound is used to find flaws and imperfections in the pipe body wall. The tool that is commonly used is stationary and the pipe is rotated and fed mechanically to examine the entire tubing body.

Hardness Test: The hardness of the tubing is usually checked when it is to be used in sour service to ensure that the tubing meets API Spec 5CT to sort mixed grads of tubing.
The recommended practices and areas where the casing and tubing inspection must address include vendor audits, quality control, expediting, laboratory test services, document control, site inspection, inspection surface preparation, Non-destructive testing, static equipment inspection, and quality control.
JC International is the nation’s leading inspection, verification, testing, and certification company. Contact us for your specific inspection requirements for your oil country tubular goods (OCTG).
Leave a Reply